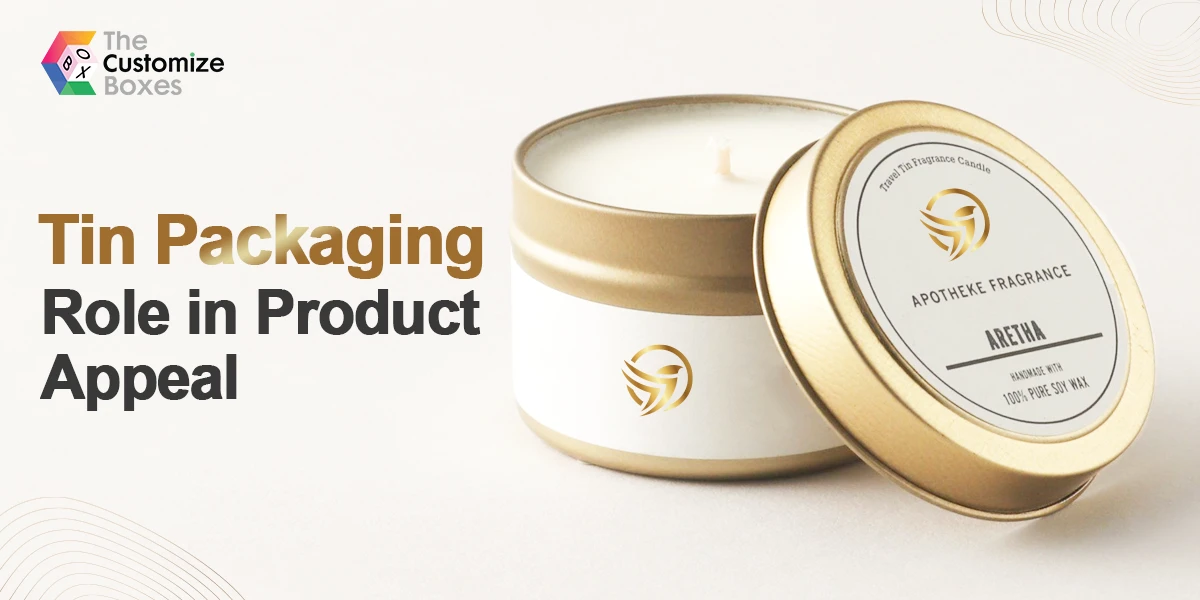
Tin Packaging and Its Role in Boosting Product Appeal
Tin packaging has had a great influence on several industries over the years. It offers superb durability to protect and preserve anything. A unique feature that makes tin packaging reliable is its versatility to accommodate products from food, beverages, cosmetics, and beyond with a touch of nostalgia.
Such exceptional features make them a good choice for brands and consumers. But where exactly did tin packaging originate from? What is the production process for tin packaging today? This blog discusses the basics, history, production process, and benefits of tin packaging – read on!
History of Tin Packaging
The concept of tin packaging started back in the early 19th century with the development of the canning process to store products for a long time. The early part of the 19th century was also known for wars, so there was a need for food preservation for long traveling scenarios and military expeditions.
A famous British merchant born in Hoxton invented tin-plated iron cans to store and preserve food items for a long time. Following that, the idea was further proceeded by Bryan Dokin and John Hall in 1813, when they officially started the production of tin cans in a canning factory. This marked the beginning of storing food in tin cans.
The production process was updated with the advancement of packaging technology. Advanced machineries were planted to streamline the production process with less effort and cost-effective means. All these efforts helped tin packaging to gain remarkable popularity over time.
Manufacturing Process of Tin Packaging
The manufacturing process of tin packaging involves several steps to ensure optimal durability, quality, and appeal. Here's an overview of the typical process followed today:
1. Material Selection
The selection of an appropriate material is the primary factor needed to perfect the packaging outcome. Tinplate is the most common material for tin packaging. It determines the durability and corrosion resistance to survive any environmental changes.
2. Printing and Coating
The printing and coating process is finalized before converting tinplate into cans. The coating adds a protective layer to your product’s tin packaging. This prevents corrosion and boosts the visual appeal. Custom printing techniques allow for personalized branding and make your packaging attractive to your target audience.
3. Sheet Forming
After finalizing printing and coating, the tinplate has to pass through forming machines where they are molded to your desired shapes and sizes.
4. Seaming or Welding
After the formation, these tinplate pieces are sealed together with the help of mechanical sealing or a traditional welding process. This process ensures that each of your tin is airtight and leak proof.
5. Quality Control
The quality control work in the entire manufacturing process ensures that each of your tins meets the industry standards and expectations. Most importantly, quality control unites the industry standards with the individual packaging requirements for the desired outcome.
6. Finishing Touches
Finally, your tin packaging is sealed and the finishing touches begin. In this process, your chosen finishing options such as embossing, debossing, engraving, coatings, printing, and lamination are added to these tins.
7. Packaging and Distribution
Once the packaging is finalized, it is prepared for distribution to retailers or directly to consumers. Secure packaging and sealing of the product itself is essential, so as to prevent damage during transportation and storage.
Benefits of Tin Packaging: Why Invest in These Packaging Solutions?
Durability: Tin packaging is known for its remarkable durability and to protect and preserve your products for a long time.
Versatility: Like other packaging variants, tin packaging is also highly customizable and can be decorated in your desired design and branding.
Brand Differentiation: Packaging suppliers provide you a free hand in customizing these cans according to your branding needs which can make your brand different from your competitors.
Visual Appeal: Tin packaging along with its quality finishing provides an attractive appearance and describes the perceived value of your products to the consumers.
Can be Resealed: Nowadays, customized tin packaging is manufactured with the feature of “resealable” lids or closures. A perfect choice for consumers who want to open and close multiple times.
Recyclability: Tin packaging is recyclable. Therefore, it’s a perfect choice for businesses prioritizing eco-friendly solutions.
Types of Tin Packaging
Usually, tin packaging is manufactured in three types to meet the branding and preserving needs of several industries:
Tin Cans: Normally tin cans are manufactured for food and beverage industries to store products such as fruits, vegetables, and beverages.
Tin Boxes: Tin boxes are prepared to pack luxury or gift items. These boxes are known for their luxurious product presentation.
Tin Containers: Tin containers are manufactured to store different kinds of products on a large scale. They are larger as compared to the other two types and they are normally found in warehouses to store a stock for a long time.
Are They Recyclable?
The tinplate material is recyclable and has almost zero negative impact on the environment. Its recyclable nature makes it the best for reusing it multiple times without losing the quality of the material. That’s why it can be a perfect option for businesses that prefer eco-friendly packaging solutions.
Wrap Up
The future of tin packaging is quite bright, as this packaging solution is completely safe for food storage and exceptional in attracting consumers. If you want to preserve your food items for a long time or want to pack your cosmetics items, tin packaging will always stand out better than others. If you have any questions about tin packaging or other packaging types, you can reach out to us anytime!